Open spray machine: the perfect supporting equipment to improve the efficiency of DTG industrial printers
Direct-to-garment (DTG) technology is widely used in the digital printing sector due to its exceptional accuracy, adaptability, and environmental friendliness. A top-notch DTG printer by itself, however, is insufficient to produce the greatest printing results; pre- and post-treatment procedures are also essential. Among these, the open spray machine is a crucial piece of equipment that supports DTG printing and can greatly increase printing quality and productivity.
1. First, what is an open sprayer?
A pretreatment tool made specifically for DTG printing is the Open Spray Pretreatment Machine. Before printing, it is mostly used to evenly spray pretreatment solutions onto textiles (such cotton, polyester, or hybrid materials). The purpose of the pretreatment liquid is to maximise the fabric's surface area for improved ink adhesion, which enhances colour vibrancy, washability, and print quality overall.The open spray machine employs an automated spraying system to guarantee that every article of clothing can be uniformly coated with pretreatment liquid, minimising human error and enhancing production uniformity as compared to conventional immersion or manual spraying techniques.
2. Open spray devices' primary benefits
(1) Boost colour performance and printing quality
Spraying uniformly: The open spray machine's precision nozzle makes sure that the pretreatment liquid covers the garment's surface evenly, preventing localised over-wetting or over-drying and enhancing ink adhesion.Increase colour saturation: By preventing ink diffusion, proper pretreatment can sharpen the design and intensify the colour.
(2) Lower labour expenses and increase production efficiency
Automated operation: The open spray machine may automatically finish pretreatment, requiring less user intervention and increasing production speed when compared to manual spraying.Suitable for mass manufacturing: It can process a lot of clothing at once to satisfy the demands of industrial-grade production.
(3) Lower expenses and preserve pretreatment liquid
Control the amount precisely: The apparatus has the ability to modify the spray volume in order to prevent waste and lower the amount of pretreatment liquid used.Lowering the rate of rework: Uniform pretreatment increases yield rate and decreases defective goods from uneven spraying.
(4) Suitable for DTG printers and a range of textiles
ideal for a range of textiles, including blended textiles, cotton, and polyester.It is compatible with DTG industrial printers of popular brands (Kornit, Epson, Brother, etc.).
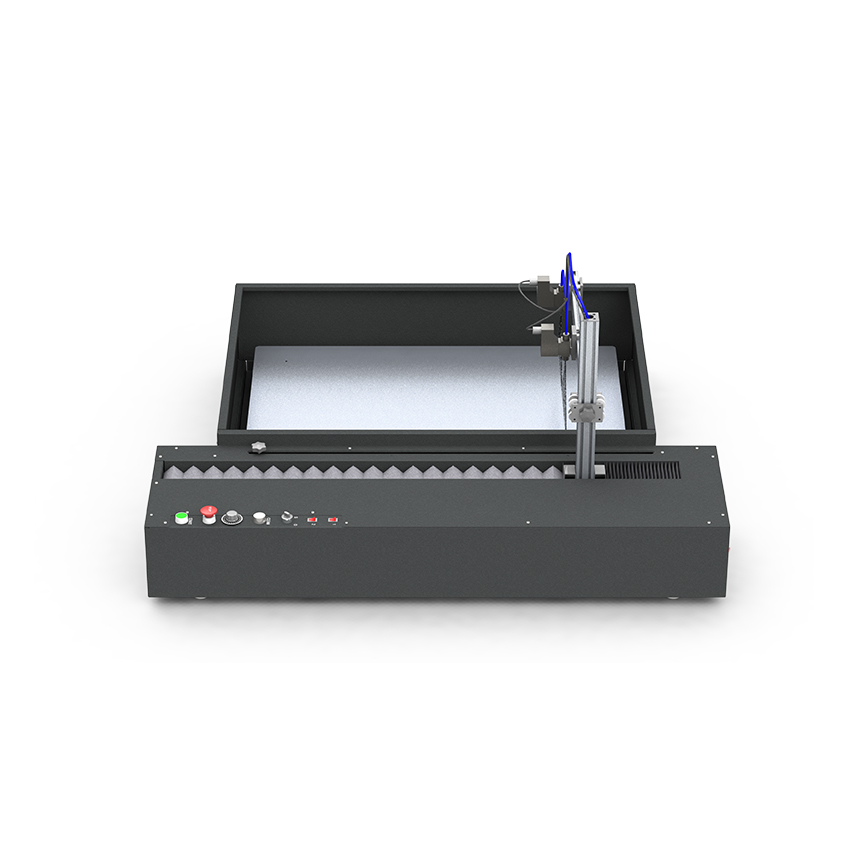
3. The open spray machine's primary performance characteristics
(1) Intelligent control system
The spray speed, spray volume, and operating mode can all be changed using the touch screen operation panel.supports one-click switching between various process requirements and sets several fabric treatment solutions.
(2) Effective spraying mechanism
Use stainless steel nozzles for long-term stable functioning because they are resistant to corrosion and difficult to clog.To prevent leaks, the multi-nozzle design covers every area of the garment.
(3) Eco-friendly and energy-efficient design
To cut down on waste, an integrated circulation system can recycle extra pretreatment liquid.Low energy consumption and noise levels are consistent with the environmental protection standards of contemporary factories.
(4) An easily maintained modular framework
To avoid blockage, the nozzle can be dismantled and cleaned.Cleaning and troubleshooting are made easier by the open architecture.
4. A comparison between the conventional pretreatment method and an open spray machine
The pretreatment technique has a direct impact on the printing efficiency and quality in the DTG (direct to garment printing) production process. These days, open spray machines, hand spraying, and immersion pretreatment are popular pretreatment techniques. They are all appropriate for various production requirements and each has pros and cons of its own.(1) Comparison of uniformity
An open spray machine increases ink adherence, prevents local overwetting or overdrying, and employs an automated spray system to guarantee that the pretreatment liquid covers the clothing evenly.
Manual spraying is labour-intensive, inconsistent, and might result in either too much or too little preparation in certain places.
Immersion pretreatment: The liquid may be unevenly dispersed after removal, impairing the subsequent printing process, even if it can completely coat the clothing.
(2) Comparison of production efficiency
An open spray machine can process huge amounts of clothing continuously and automatically, greatly increasing manufacturing speed.
Manual spraying has a sluggish speed, relies on human skill, and is challenging to meet medium- and large-scale production demands.
Immersion pretreatment is appropriate for small and medium-sized batch orders, although it requires more drying time and has a medium production efficiency.
(3) Pretreatment liquid consumption comparison
Open spray machine: Accurately regulate the spray volume, cut down on waste, and save money over time.
Spraying by hand: It is challenging to precisely regulate usage, which frequently results in liquid waste.
Pretreatment by immersion: To soak the garments, a lot of pretreatment liquid is needed, and a lot of liquid is used.
(4) Evaluation of the relevant production scale
Open spray machines can be easily integrated into the DTG printer assembly line and are best suited for large-scale, industrialised production.
Manual spraying is only appropriate for producing samples or small batches; it is challenging to use on a big scale.
Though less effective than a spray machine, immersion pretreatment is appropriate for medium-scale operations.
(5) Convenience of operation comparison
The spray machine is open. reduced technological obstacles, preset mode support, and one-button operation.
Manual spraying: Depending on the experience of the workers, poor performance might quickly degrade quality.
Immersion pretreatment: This method is more laborious and requires manual control of the soaking and drying procedure.
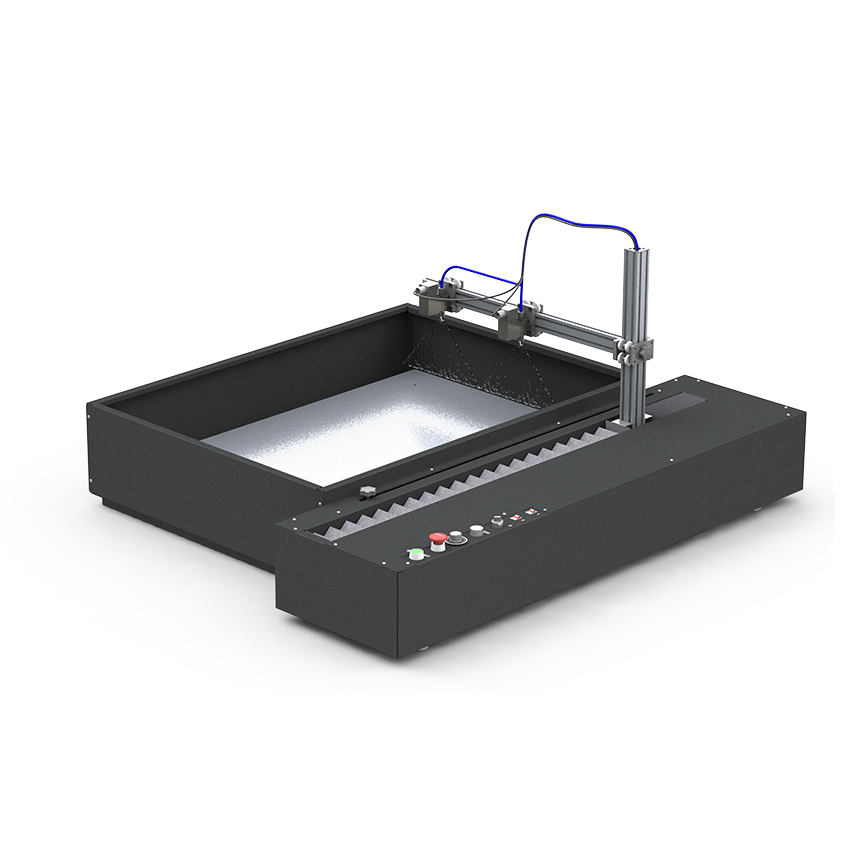
5. How does a DTG industrial printer interact with an open sprayer?
(1) Standard procedurePlacement of clothing: Hang the garments on the conveyor belt of the sprayer or lay them flat to be printed.
Automatic spraying: The pretreatment liquid, often an aqueous solution, is sprayed uniformly by the apparatus.
Drying and curing: To solidify the pretreatment liquid, the sprayed clothing is either dried naturally or placed in a dryer.
The DTG printer receives the pretreated clothing and prints it.
Post-processing: To enhance washability, heat press curing is done after printing.
(2) Crucial elements for production line optimisation
Keeping the printing and spraying speeds in line: To prevent bottlenecks, make sure the DTG printer's and the sprayer's production capacities are in sync.
Managing the recipe for the pretreatment liquid: To get the optimum printing result, modify the pretreatment liquid composition based on the kind of fabric.
Maintain the nozzle on a regular basis: Avoid obstructions and guarantee consistent spraying.
6. Relevant clientele and industries
The following industries make extensive use of open spray machines:T-shirts, sweatshirts, sportswear, and other items can be customised with the help of garment printing factories.
Manufacturers of promotional products: creation of commemorative shirts for events, corporate gifts, etc.
Fashion brands: high-end, customised apparel made in small batches.
E-commerce printing service providers: enhance delivery speed and satisfy the demands of quick orders.
7. How can I pick an appropriate open sprayer?
The following elements must be taken into account when buying an open spray machine:Requirements for capacity: depending on the typical daily production, select a model that is the appropriate size and speed.
Verify compatibility with current DTG printers and drying apparatus.
Select a trustworthy source to guarantee technical support for both brand and after-sales care.
Improved scalability: some expensive models have the capacity to connect to the MES system in the future and offer intelligent networking.
RECENT POSTS
-
Open spray machine: the perfect supporting equipment to improve the efficiency of DTG industrial printers
-
The Perfect Partner To Improve DTG Printing Efficiency--Enclosed Spray Machine
-
Industrial Printer Maintenance Guide: Keep Your Equipment Running Smoothly
-
Which Printing Type is the Most Cost-Effective for Large Print Jobs?
-
What Is The Difference Between Wide Format And Large Format?
Application
-
DTF Printer Effect ShowDirect to film printer(DTF printers) are T-shirt transfer printers,Hstar DTF printer offer a transfer solution especially for dark color fabric,which is a creative application process.
-
Vango DTF printerOur DTF printer adopts an all-in-one printing design, which is more space-saving and easier to operate.This is our printing show.
Wide applications,design for textile printing,Suitable for all kinds of fabrics, T-shirts,leather, bags and shoes etc.
More Application